ABOUT US
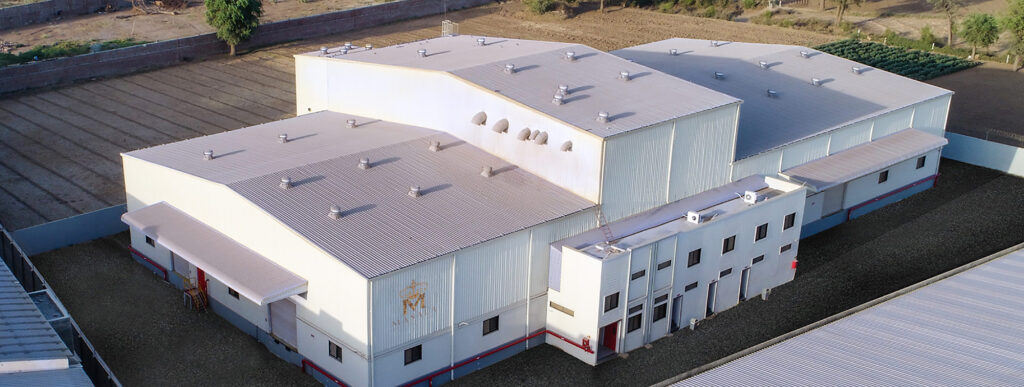
STATE OF THE ART INFRASTRUCTURE
Masala Majesty recognized the importance of modernizing our production methods early on. Over recent years, we’ve made significant investments in our infrastructure to optimize our manufacturing processes. In Unjha, Gujarat, we’ve established a cutting-edge, eco-friendly facility equipped with state-of-the-art machinery such as the Buhler Sortex Plant, Hi-Tech Powder Plant, QC Laboratory, Fully Automatic Packing Machine, and Inkjet Printing Machine.
Situated in Unjha, known as the largest market yard in Asia for commercial cash crops and dubbed the Spice City of India, our factory spans 5000 Square Meters and comprises various departments. Our facility boasts advanced machinery and a well-equipped infrastructure, including the fully automated Buhler Sortex Machine, Flavor lock Grinding Powder Plant, Packing Machine, and in-house laboratory. These automatic systems handle cleaning, grading, color sorting, grinding/pulverizing, blending, metal separation, and packaging processes.
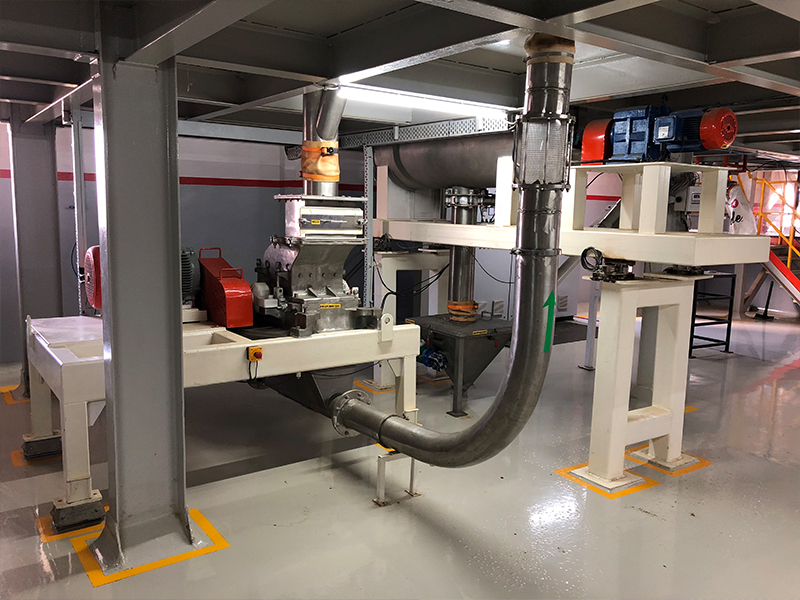
FULLY AUTOMATED GRINDING
Masala Majesty employs cutting-edge flavor lock grinding technology, which rapidly freezes spices to preserve their natural flavor and color. This grinding method operates at sub-zero temperatures, typically ranging from 0 to minus 70°F, without altering the spices’ chemical composition. Unlike traditional grinding techniques, our process begins with air-dried spices rather than freeze-dried ones, resulting in superior natural color retention. This approach ensures finer particle sizes without sacrificing aroma or causing color changes, making it essential for all spices.
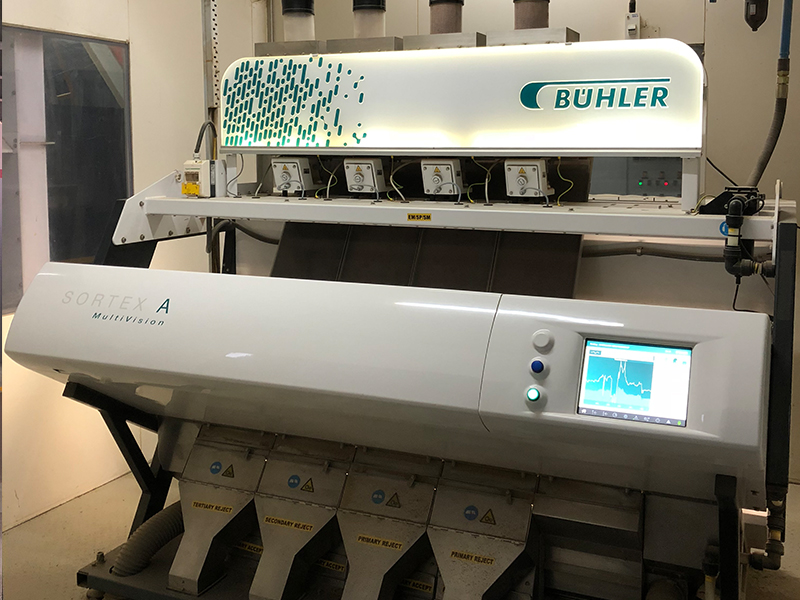
CLEANING AND SORTING
Masala Majesty utilizes a Buhler Sortex Machine to meticulously clean, grade, and sort spices by color. This machine ensures that raw materials are refined into the highest quality whole and ground spices.
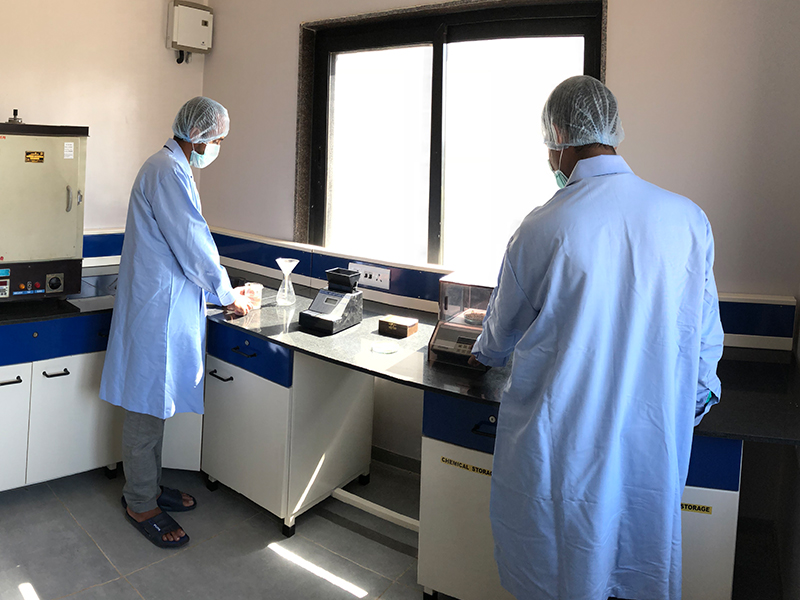
NABL STANDARD LABORATORY
We maintain an in-house laboratory compliant with the National Accreditation Board for Testing and Calibration Laboratories (NABL) standards. Our fully functional laboratory conducts physical, chemical, and microbiological tests using state-of-the-art equipment and trained analysts at three crucial stages: during spice collection, production, and final product packaging. These tests adhere to both national and international standards. To stay current, we regularly update our equipment and testing procedures to align with evolving food safety regulations, ensuring that we consistently provide exceptional value to our customers.
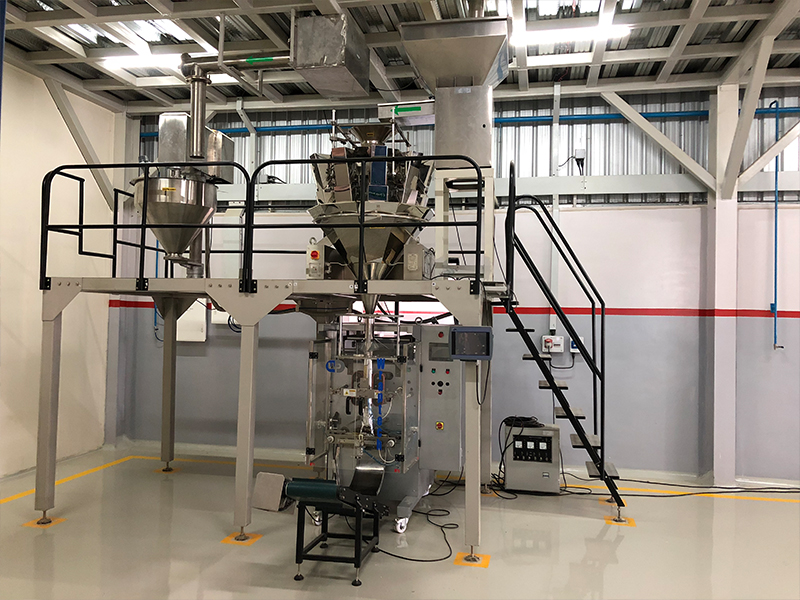
AUTOMATED PACKAGING MACHINE & INKJET PRINTING
The automated machine is equipped with a continuous flat roll of poly pouch, featuring labeling and artwork on its exterior surface. It’s worth noting that although plastic is the predominant packaging material in the food industry, this technology can also accommodate continuous metalized foil/film, paper, and fabric containers by adjusting the edge sealing/seaming methods. The automatic packing machine is capable of handling packaging ranging from 50gm to 5kg.
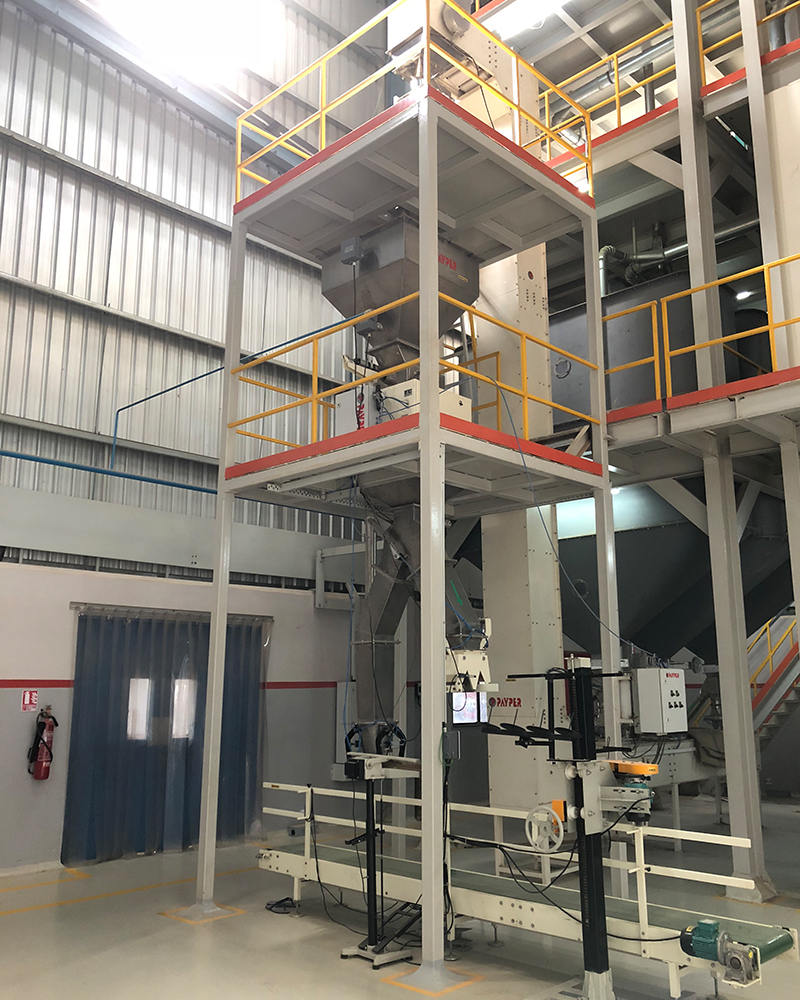
AUTOMATIC BAGGING SYSTEM , STITCHING AND WEIGHER MACHINE
Masala Majesty’s automatic bagging machines are designed to efficiently handle various types of bags, catering to the packaging needs of bulk solid products such as granules, powder, whole spices, larger particles, and flakes, with unit weights ranging from above 50gm to Jumbo Bags.
These machines are compatible with:
- Open Mouth Pre-made Bags: Including paper bags with lamination and liner, woven bags with lamination and liner, and plastic bags. Closure options include stitching, heat sealing, or a combination of both.
- Form-Fill-Seal: This versatile machine forms the bag, seals the bottom, fills the product, and seals the top. Bags are made from heat-sealable plastic materials and tubular coils (PE, PP, or compounds).
- Valve Bags: Available in paper, plastic, or woven materials, these bags are primarily used for filling bulk solid products. They feature a valve through which the product is filled, which can be self-closing or sealed by an ultrasonic sealer.
- FIBC Jumbo Bags: Suitable for both net and gross weighing operations, these bags can accommodate various outputs and products. They can be used for filling Jumbo Bags, Octabin, Totabin, etc., with capacities ranging from 200 kgs to 2000 kgs.
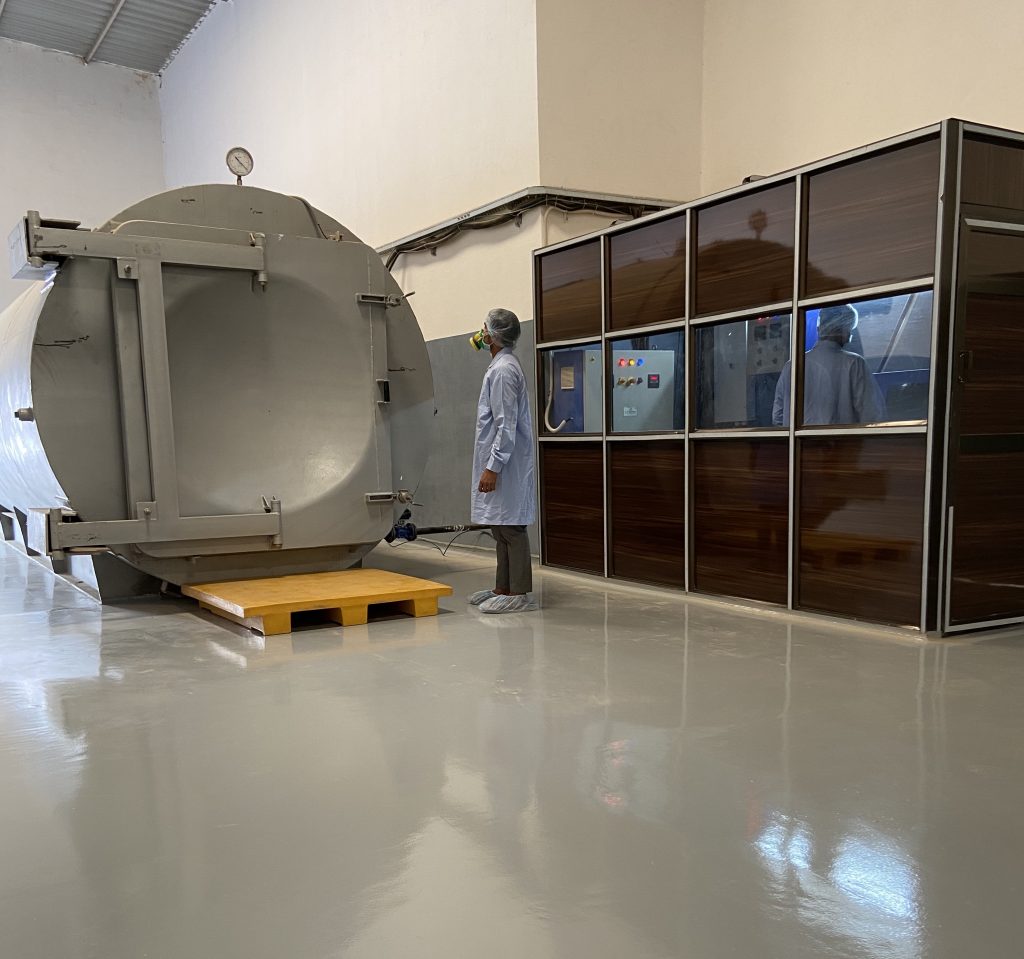
Ethylene Oxide Plant
Ethylene oxide (EO) treatment is employed to significantly reduce the bacterial population in spices by up to 90%, effectively eliminating bacteria, fungi, viruses, and bacterial spores. This process involves placing the products to be sterilized in a sterilization chamber and exposing them to sterilant gas at specific temperature, humidity, and pressure settings.
The objectives of EO sterilization are as follows:
- Eradicate pathogenic and other detrimental microorganisms and bacterial spores.
- Mitigate potential salmonella contamination to a level deemed safe for human consumption, typically achieving a 5-log reduction.